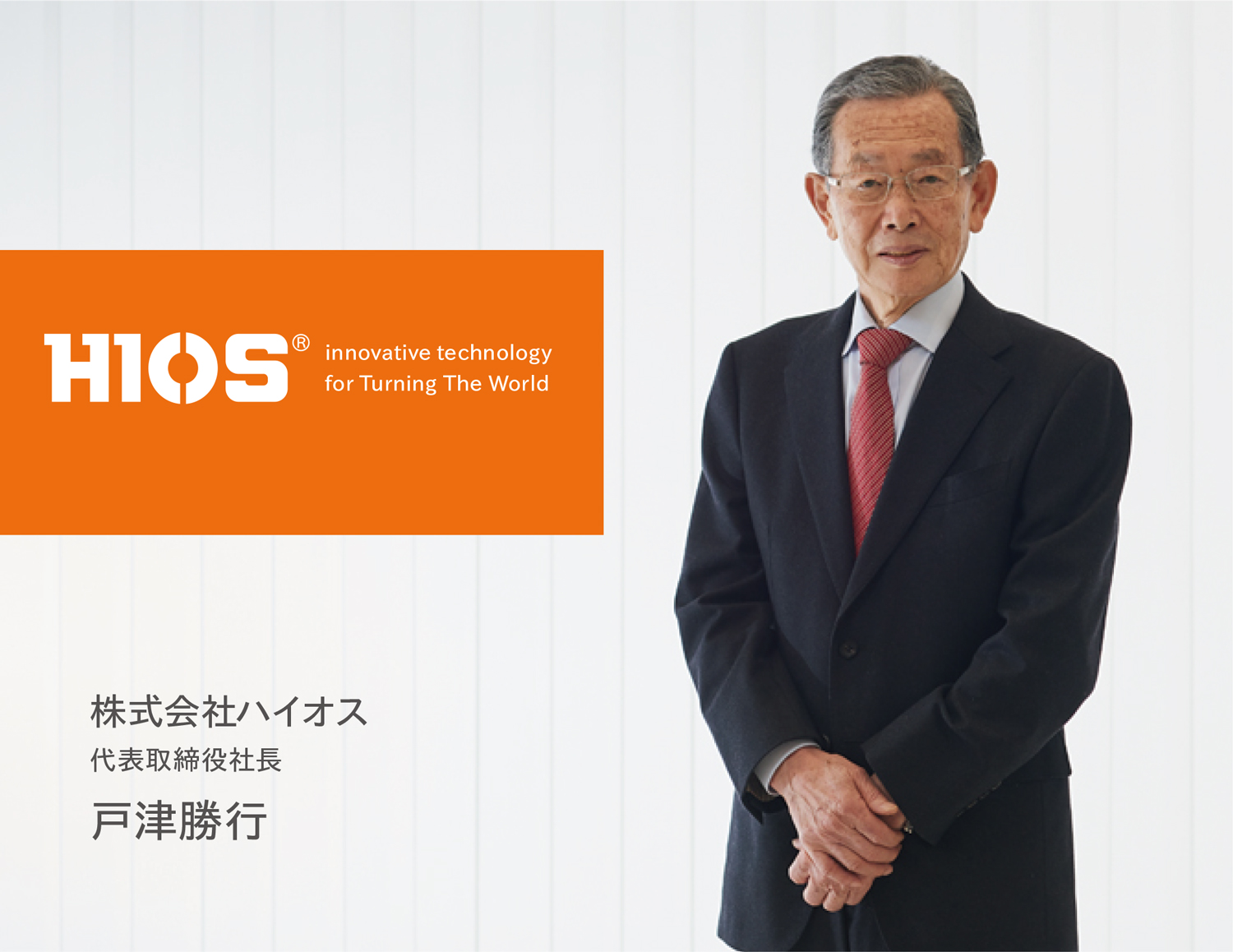
「環境」という言葉が産業界でそれほど語られなかった時代から、ハイオス(HIOS、東京都墨田区)は、製造現場の環境改善につながり、省資源・省エネルギーに配慮した製品開発を進めてきた。
同社は産業用電動ドライバーのパイオニア。戸津勝行社長は1970年の設立から「業界初」「世界初」となる画期的な製品を投入し続け、生産の変革に貢献してきた。
世界初の産業用電動ドライバー 低電圧の「安心・安全」性能、ねじ締め効率が大幅向上

前身の戸津研究所時代、1967年に世界に先駆けて産業用電動ドライバー「M型ドライバー」を発売。前年に考案した「トツねじ」はねじ中央部の凹みと、ドライバー先端(ビット)の凸部で、ねじとビットの嵌合(かんごう、はまり合い)性能を格段に引き上げた製品。これらと、ねじを簡単に装着できる「自動チャッキングビット」と合わせた「HIOSYSTEM (ハイオシステム)」は、ねじ締めの作業効率を圧倒的に向上させた。
M型ドライバーは精工舎(現セイコー)の高精度振動子時計やナショナル(現パナソニック)の世界初1インチブラウン管マイクロテレビ、ソニー(現ソニーグループ)のラジカセなどの製造に次々採用され、生産拡大に大きく貢献した。
特に1980年に任天堂が発売した携帯ゲーム機「ゲーム&ウオッチ」の爆発的な増産に、チャッキングが可能なトツねじを使用した同社のねじ締めシステムが果たした役割は大きい。
ハイオスの電動ドライバーの画期性は、電流電圧制御でドライバーのトルク(締め付け力)管理ができるようになった点。主婦が内職でねじ締めする際も、ダイヤル式でトルク調整が簡単に行えるため、指示書通りに作業することで完全な品質管理が可能になった。しかも、最大28Vの低電圧で家庭に持ち込んで子どもが触れても感電の心配がなく、動作音も静か。こうした「安心・安全」性能は、社業の初期からハイオス製品の特長だ。
環境に配慮した製品開発にも、創業当時からこだわる。ビット先端部が磨耗しても、刃先だけ交換すればビットホルダーを繰り返し使用できる省資源性もその一つ。当時の生産現場では、ビットが磨耗すると、ビットごと捨ててしまうのが普通だった。トツねじと自動チャッキングビットの組み合わせで、廃棄ロスは大幅に削減できるようになった。
充電式ドライバー 欧州の大手自動車が採用、NASAからも製作依頼
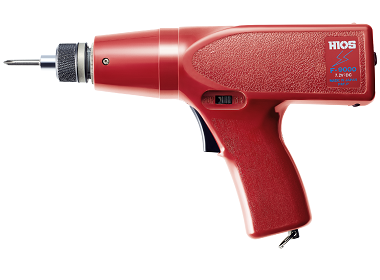
今では当たり前の充電式ドライバー。これもハイオスが1979年に世界で初めて製品化した(充電式ドライバー「Fシリーズ」)。
当時、広く使われていたのは空気圧を用いたエアーツール。生産ラインが移動すると空気を送るホースを延長しなければならず、自動車のボディなどの製造品を傷つける恐れがあった。ホースの不要な充電式ドライバーはフォルクスワーゲン、BMWなど欧州の大手自動車メーカーで大量に導入。評判は世界各地に伝わり、1996年にはNASA(米航空宇宙局)から宇宙空間で使用できる充電式ドライバーの製作依頼が舞い込む。結果的に、割ける経営資源に限界があったことから辞退したという戸津社長。「目の届く範囲で良い物を開発していきたかった」と当時を振り返る。
エアツールに対する電動ドライバーの利点は環境面にもある。
エアツールはコンプレッサーで圧縮した空気を排出してタービンを回す。この排出した空気には水分や油などが含まれ、それらはカメラのレンズなど製品に付着してカビの原因になる。排気は人体への影響も。「クリーン」であることは電動ドライバーの大きなメリットだ。
ブラシレスモーターをドライバーに応用 トルク精度と耐久性も大きく改善
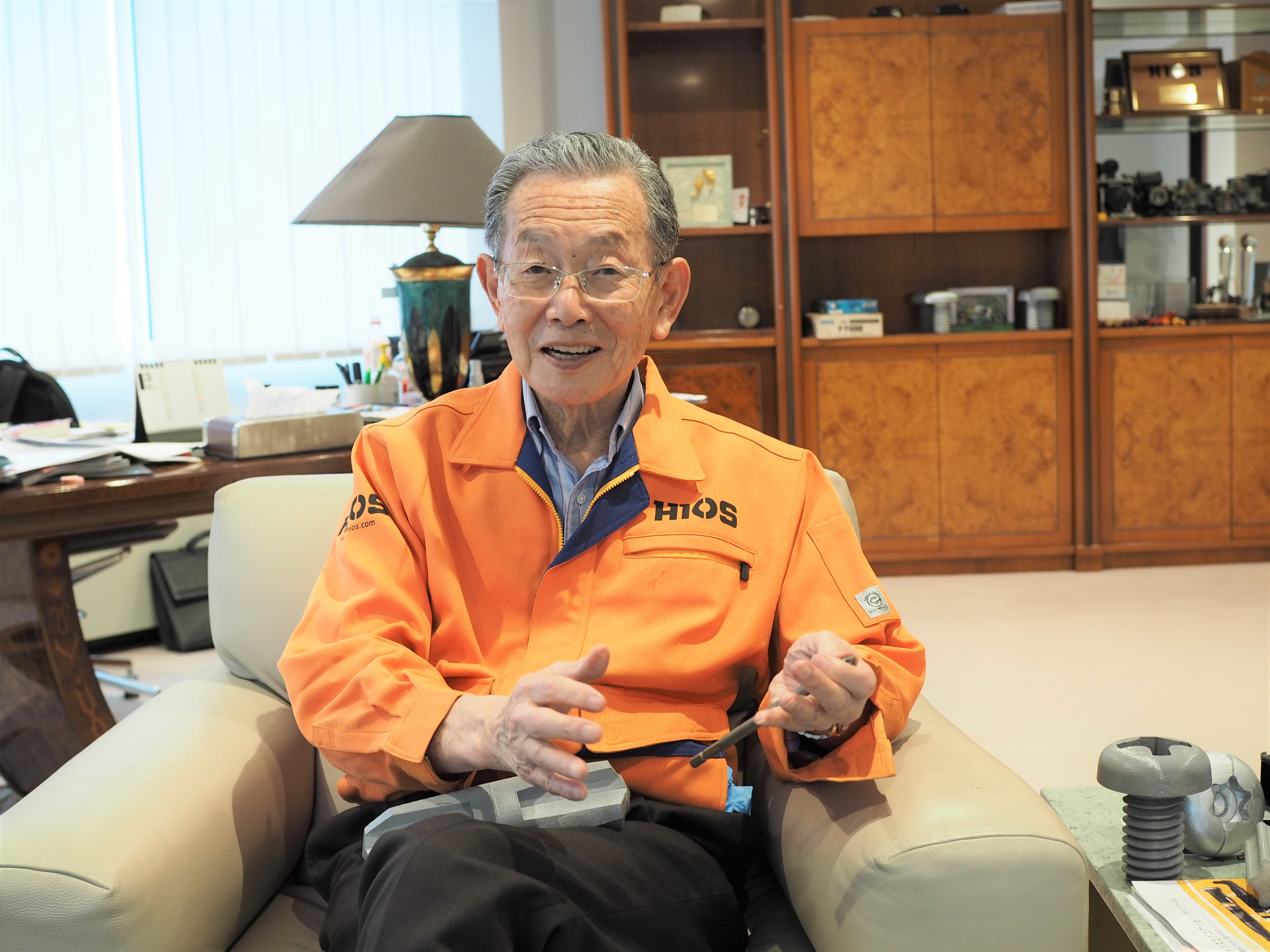
高効率で小型化が可能なブラシレスモーター。車載向けをはじめ、さまざまな製品に搭載されているが、これをドライバーに応用したのはハイオスが業界初。2001年にブラシレスドライバー「BLシリーズ」を発売した。
ブラシの摩耗がないためカーボン粒子が排出されない。ブラシ付きの場合、ドライバーの内部は排出されたカーボンが付着して真っ黒になった。ブラシのこすれる騒音や電気ノイズも生じず、ドライバーのトルク精度と耐久性も大きく向上できるのがブラシレスドライバーの強み。さらに安定した品質管理が可能になった。
デジタルドライバー「熟練工シリーズ」 ねじ締め作業時のエラーを自動検知
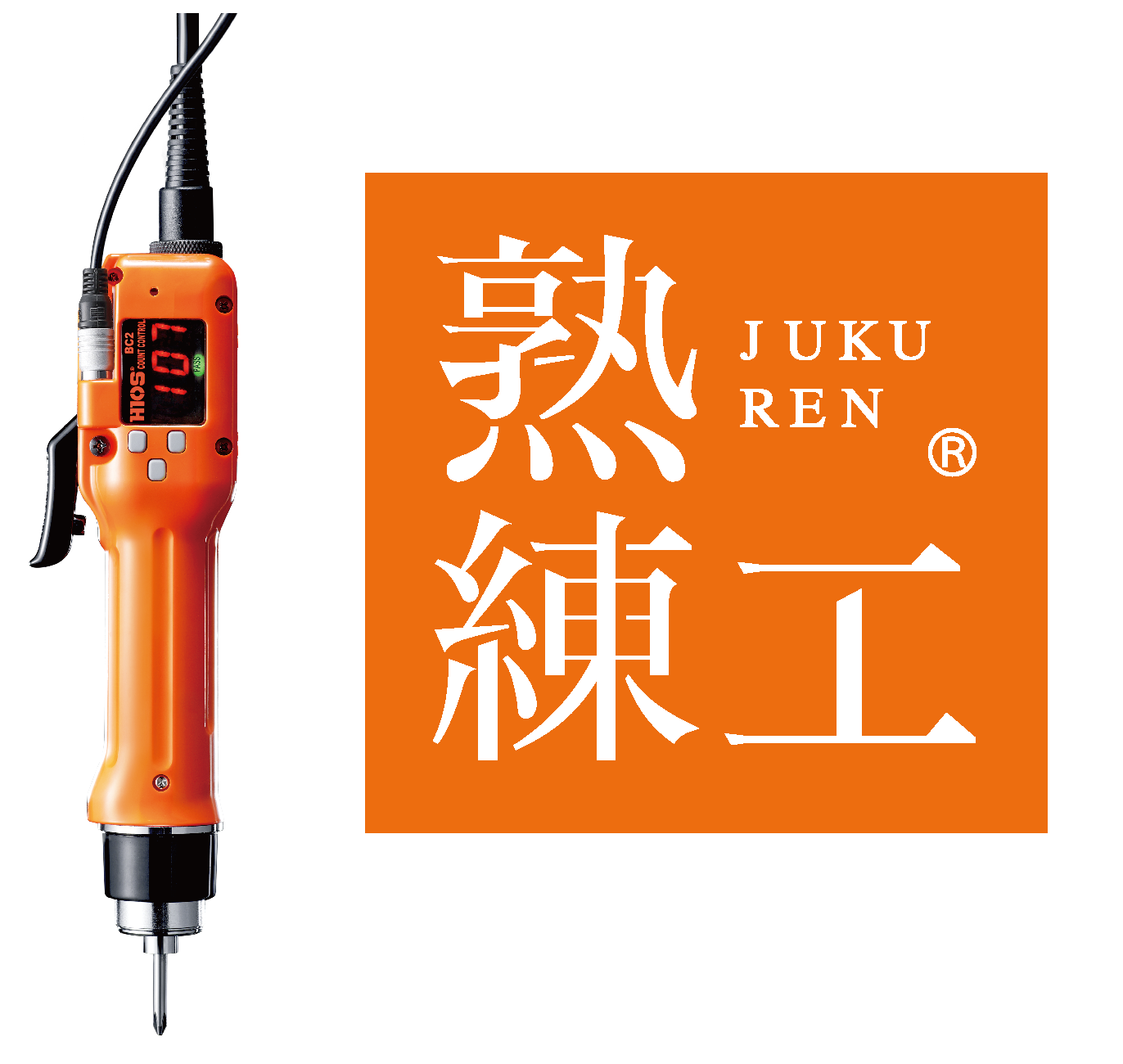
ねじを締め付ける工具に過ぎなかったドライバーは、ついにIoTの世界にまで発展する。
ブラシレスモーターは、ホール素子(磁気センサー)と電子回路で電流の切り替えを行う。この時、モーターから発信される信号を読み取ってパルスの数を数えることで、ねじ締め付けの状態をドライバー自身が判断できるのがデジタルドライバー「熟練工BLG-BC2シリーズ」だ。
パルスシステムを内蔵し、ねじ締め開始から着座までのモーターの回転パルス数をカウント。これにより「ねじが完全に締まっていない」「誤ったサイズのねじが入った」といったねじ締め作業時のエラーをリアルタイムで検知できる。戸津社長は「作業者ではなく、ドライバーがねじ締めの合否を判断し、品質管理する」と熟練工の究極的ともいえる性能を説明する。
IoTへ進化 ねじ締めのトレーサビリティーが可能に
IoTへの進化で、電動工具の可能性は飛躍的に広がった。
ねじ1本1本の締め付け状況をデータ化できるため、ねじ締めのトレーサビリティー(生産履歴の追跡)が可能になる。複合機1台には数百本のねじが使われるが、各ねじの締め付け状況の履歴は残されず、ねじは「締めっぱなし」なのが現状だった。
戸津社長は、大手メーカーが熟練工を利用した際、「ねじ締め不良率の多さに驚いていた」と語る。それだけ従来の締め付け作業ではNG品が多く出ていたということになる。熟練工であれば、締め付けごとに手元のパネルに測定値が表示されるため、その場で合否の判定ができる。
IoT化に伴いデータはクラウド上での一元管理に発展する。グローバルに展開する企業の複数拠点の生産状況をリアルタイムで管理し、膨大な生産履歴を元に、従来は不可能だった生産の精緻な分析と対策が行えることになる。
「究極のドライバー」でねじ締め不良を「根絶」
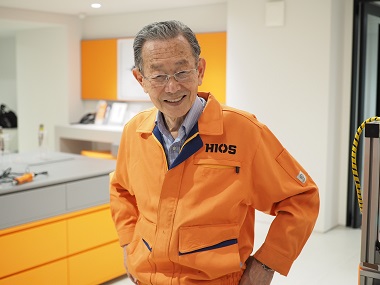
誰でも使ったその日からマイスターになれる―。
デジタルドライバーによるねじ締め不良の「根絶」は、作業者の熟練度を問わず、高品質な製造を実現する。それは雇用や労働の問題の解決に果たす役割も大きいと戸津社長は指摘する。
ねじ締めは単調な仕事。長時間続けると作業者のストレスもたまり、ミスがあれば自分の責任になる。これでは従業員の定着率も上がらない。自動でドライバーが合否判定する熟練工なら業務負荷だけでなく、作業者の心理的な負担も軽減されるというわけだ。モーターの温度上昇を30%抑制し、消費電力は50%削減するなど、省エネルギー性能も高い。戸津社長自ら「ドライバーのほぼ究極の形」と自信を見せるのも無理はない。
次世代ねじ「インタトルク」 嵌合時のぐらつきを防止
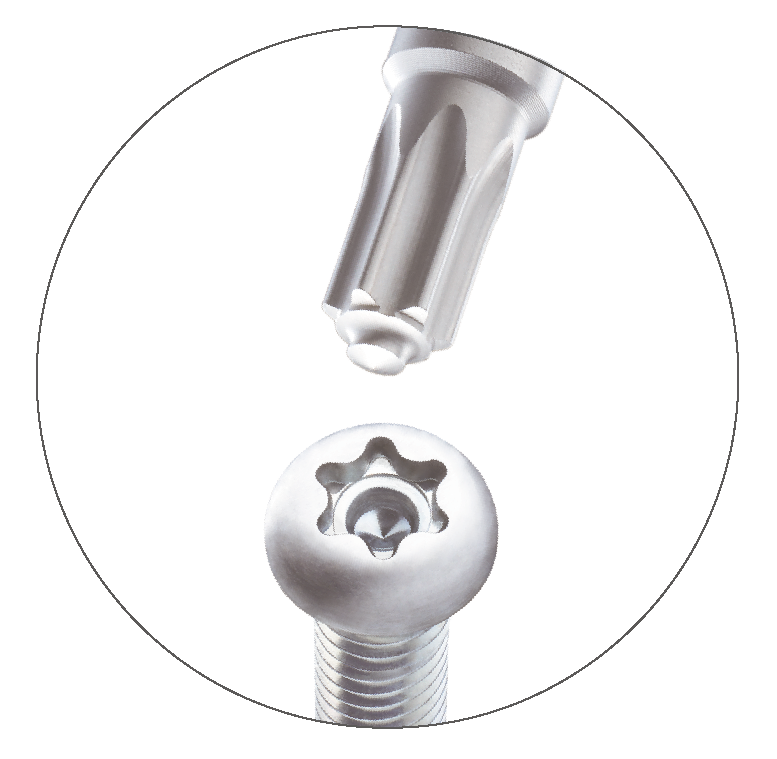
ねじ締め作業はドライバーとその先端部であるビット、ねじの3要素で構成される。ハイオスは創業以来、ドライバーとともにねじの開発にも力を注いできた。
1999年に販売開始したのは十字ねじを改良した「トツプラねじ」。ビットがねじの溝から浮き上がってしまう「カムアウト」を防ぎ、作業性を向上させた製品だ。ビットが浮き上がらず、上から押し付けずに回転力だけで締め付けできるため、作業者の疲労は軽減。ビットの磨耗が減って寿命も延びる。
そして、2008年にリリースしたまったく新しいねじ「インタトルク」は「過去数十年の開発の中でベストな製品」と戸津社長は太鼓判を押す。
溝が花びら形状のねじで、回転力が加わるとビットが自動的に凹みに向かって移動して嵌合できる。最大の特長は嵌合時のぐらつきを防止してねじ締め時の安定性が維持できるところ。ねじ締め不良がなくなり、ねじ自体のロスだけでなく、製品部材の破損などのワークロスが低減できる。
この「押し付ける力」という余分なエネルギーが不要なため、ねじ締めロボットの小型化にもつながるという。
「人より一歩先」の50年 視線は「カーボンニュートラルの実現」に
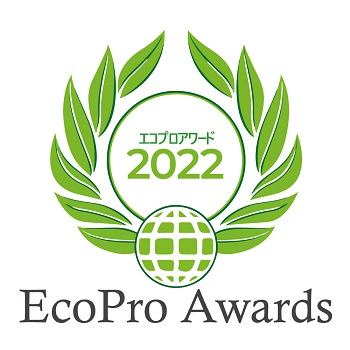
このほど、同社の一連のねじ締結システムが「製品ライフサイクル全体の環境負荷削減に貢献する」として、第5回エコプロアワード「奨励賞」を受賞。創業時から一貫した環境への取り組みにあらためてスポットライトが当たった格好だ。
これまで、ねじを「締める」にこだわってきた同社。戸津社長は、今後、解体やリサイクルの省力を考え、「緩める」について考えたいと意気込む。
50年以上にわたり「人より一歩先を読む」の実践をたゆまず続けてきたハイオス。視線はさらに前を向く。その先に見据えるのは「カーボンニュートラルの実現」だ。