2022.03.07 【SMT/SMD特集】 SMD、小型・高機能化が加速
プリント基板の高密度化に対応して小型・高機能化が進むSMD
表面実装技術(Surface Mount Technology=SMT)の高度化を背景に、チップ部品(Surface Mount Device=SMD)の技術進化が目覚ましい。5G(第5世代移動通信規格)スマートフォンやIoT端末、自動車のECUや各種モジュールにおける高密度実装化ニーズの高まりが、SMDの小型・高機能化を加速させている。
高密度実装ニーズに対応
SMDのグローバル需要は、新型コロナ拡大に伴う2020年前半の低迷を経て、20年夏場以降、需要が回復。以来、想定を上回るペースで需要が増大し、21年も年間を通じて好調に推移した。自動車や産業機器の需要回復や堅調なハイエンドスマートフォン、リモート・巣ごもり関連需要などがSMDの成長を支えている。足元で半導体不足による完成品生産への影響が表面化する中でも、多くの分野で堅調さが続いている。
22年も堅調の見込み
SMDの需要は、22年も堅調な推移が見込まれる。SMD各社は今後も機器の小型・高機能化に向け、積極的な新製品開発を推進する。生産体制増強の動きも活発化している。
製品別では、抵抗器は自動車のADASや電動化に照準を合わせた新製品開発が進展。5GスマホやIoT端末向けの超小型品開発にも力が注がれる。
5Gスマホ向けは、0603サイズ、0402サイズの需要が伸びる見通し。電源回路では、電流検出用途で低抵抗チップが用いられ、中でも金属板タイプが伸びている。最小は1005サイズ。
モジュールでは部品内蔵基板で小型化する動きも見られる。銅めっき接続方式では銅めっき電極を形成した専用部品が必要で、チップ抵抗器では厚みが0.13ミリメートルまで極薄化している。次世代チップとして、0201サイズも提案されている。
車載では、電源周辺部の回路向けに硫化に強く、硫化発生による抵抗値断線を防ぐ耐硫化チップ抵抗器が使用される。エンジン制御回路のほか、各種ECUなどでは耐サージチップ抵抗器が搭載される。金属板抵抗体が製品ボディーを兼ねるパワー低抵抗チップ抵抗器の大電流、ハイパワー、低抵抗化技術も進展している。
積層セラミックコンデンサー(MLCC)は、車載向けに低損失、三端子、共振用、高耐熱、高電圧、大容量化への開発が進む。5G用では、0402/0603サイズなどの超小型品の大容量化が進む。0201サイズでは、0.1μFまで大容量化が進展。基板内蔵用は、厚み0.064ミリメートルまで極薄化している。
アルミ電解コンデンサーは、電解液タイプに加え、ポリマータイプ、ハイブリッドタイプのラインアップが充実化。ポリマー系は、車載、5G基地局向けの需要に対応する。ハイブリッドコンデンサーは、低ESR、高信頼性の高耐電圧が特徴。ECUなどでの採用が本格化し需要が急増している。最近は150度対応品投入も進んでいる。
インダクターも5Gや車載を中心に技術革新が進む。高周波インダクターは、高Q化、高精度化と小型化を兼ね備えた製品が要求される。現在は0402サイズでの高Q化技術が進展している。
電源用パワーインダクターは、フェライト巻線型、フェライト積層型のほか、近年はメタル系パワーインダクターでの巻線、積層、薄膜があり、1608サイズなどの小型化が進展。メタル積層チップパワーインダクターは1005サイズも製品化されている。車載用インダクターは信頼性が強く求められ、ECU用では125度対応から150度対応へと耐熱技術が高度化。180度対応品も開発された。
車載用温度センサーの技術開発も活発。1005サイズで、マイナス55~プラス150度の使用温度に対応し、抵抗が最大100kΩの導電性接着剤実装用チップNTCサーミスタなども開発されている。
SMT、スマートファクトリー化
装置間つなぎ高品質生産を実現
SMTは、電子部品の発展とともに進化を続けている。
電子部品にはリード線の付いたリード部品(DIP部品)とSMDがある。リード部品はプリント基板の穴(スルーホール)に実装するが、SMDは基板の表面に部品を搭載してはんだ付けする。
SMDのサイズはEIA(国際電気標準会議)とJISによる規格があり、角型チップ部品では数字をベースとした呼び名を持っている。
JISではミリメートルが基本で0.6×0.3ミリメートルのSMDは「0603」、EIAではインチが基本で0.6×0.3ミリメートルのSMDは0.0236×0.0118インチなので「0201」となる。日本国内では通常JISが用いられる。
1955年ごろにトランジスタが登場して、リード線の付いた電子部品をプリント基板の穴に挿入してはんだ付けする「スルーホール技術」へと変わり、部品挿入機が全盛の時代が続いた。90年ごろにプリント基板の表面に電子部品を搭載するSMTが開発され、現在はプリント基板製造工程の主流になっている。
SMTは電子部品をテーピング装置でテープフィーダーに装着し、実装機(マウンター)でテープフィーダーから部品を1個1個、空気で吸着し、銅箔(はく)で配線が描かれたプリント基板の表面に部品を誤差マイクロメートル以下という高精度で、1秒間に30~40個の部品を搭載する。その後にリフローではんだ付けを行う。
SMTはスマートフォンの登場で劇的に進化した。スマホの小型化のために微小な0201サイズのSMDが開発され、同時にプリント基板の配線も高密度化が一気に進んだ。また、モジュール部品も多様化。このことから、スマホの大量生産には高速化が不可欠になった。
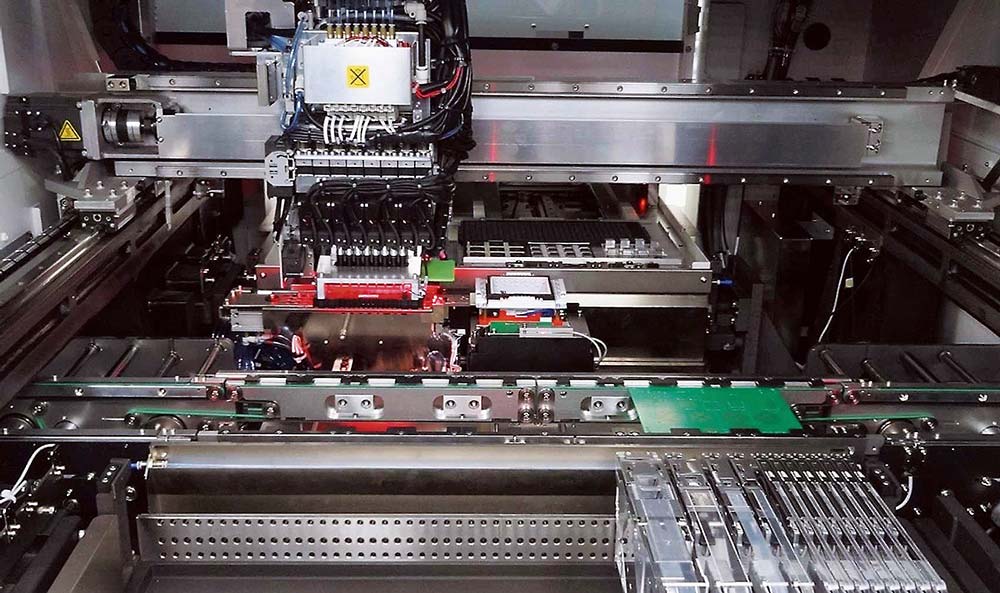
これらの動きに対し、実装機各社は多ヘッド化、多ノズル化、ヘッドの軽量化、XYロボットへのリニアモーター採用、モーター駆動フィーダーの採用、基板・部品認識処理速度の向上などを課題として取り組んできた。
ドイツが提唱する第4次生産革命「インダストリー4.0」に端を発して、製造業におけるIoTへの関心が急速に高まった。SMT業界では実装ラインの装置をつないで(M2M)データ化することで、無駄のない効率的な生産ラインや工場づくりを実現する「スマートファクトリー」が実装各社の事業戦略の柱になってきた。
スマートファクトリーはIoT、AIなどの技術と組み合わせ、装置と装置をつないでデジタルデータをやり取りすることで、人手を介さずに装置自体の自己完結型で高品質生産の実現を目指している。将来的には無人工場が実現する。