2024.01.09 【製造技術総合特集】24年、市場拡大が期待される生産設備 CNに貢献する設備など注目
低温はんだ付け材料群
2024年はこれまでの部材不足が続いたサプライチエーンが正常化し、同時に製造業の設備投資再開の期待もあり、生産設備産業も活気を取り戻すとの予測が多い。カーボンニュートラル(CN)に貢献する設備や、生産自動化を加速する装置など需要の拡大が期待される。
低融点はんだ
CO₂削減の取り組みが本格化
はんだ業界は「熱」を扱うだけにCO₂削減に対する関心が高く、SMT業界と連携しながらカーボンニュートラルに貢献するさまざまな取り組みを本格化している。
はんだ付けの接合プロセスは、フラックスによる「酸化被膜除去」の後、母材とはんだにおける「ぬれ」「溶解」「拡散」によって達成される。酸化被膜が除去された金属表面に溶融したはんだがぬれ広がり(ぬれ)、はんだ成分中へ母材の金属成分が溶け込む(溶解)。金属成分が溶解する過程ではんだ材と母材の原子が相互に移動することによって金属間化合物が形成される(拡散)。この溶解と拡散によってはんだの金属間結合が達成される。中でも「濡れ性」は製品の機能性や安全性に大きく影響するため、はんだ付けの欠かすことのできない特性になる。
はんだ付プロセスの温度を下げることは、結果的にCO₂削減につながる。はんだは合金であり、組み合わせる金属組成によって融点が異なる。これまでJEITAが標準組成として推奨してきたSn+Ag+Cu系の「SAC305」(Sn-3.0Ag-0.5Cu)の融点は217度だが、一般的には220~250度のはんだが用いられる。融点を下げることは、はんだ槽の省電力化や実装工程の効率化、実装デバイスのダメージ軽減など利点が多く、その結果がカーボンニュートラルにつながる。はんだはBi(ビスマス)In(インジウム)Cd(カドミウム)などが含有されると融点が183度未満に下がる。こうした低融点はんだを使用したソルダリング工法をSMT業界に本格的な提案を始めている。
ハロゲンフリーも進む。従来はフラックスのはんだ粉や松ヤニ成分に、活性成分としてハロゲン化物を添加していた。
ハロゲン元素を含んだものは燃焼(廃棄時の焼却)することで、毒性の高いダイオキシンや酸性雨の原因にもなるハロゲンガスを発生する。ハロゲンを抜くことで懸念されるぬれ性・溶融性の低下に、新たな活性剤として有機酸やアミンなどが用いられるようになっている。
リニアコンベヤーモジュール
製造現場の次世代型搬送システム
リニアコンベヤーが製造現場の次世代型搬送システムとして注目されている。
モジュールは従来のベルトコンベヤーやローラーコンベヤーに比べて、製造現場などのラインの組み替えが簡単・自由に行える上、高速・高精度の搬送が可能で幅広い業界に適用できる。FAで利用されるリニアモーターの構造は、一般的な回転型モーターを直線状に引き延ばしたもので、磁石のN極とS極が交互に直線状に配置されている。このリニアモーターのコイル部分に電流を流すことで交番磁界を発生させ、磁気吸引力や反発力から直進方向の駆動力を得ている。
リニアコンベヤーモジュールは、リニアモーターとスライダー、コントローラーを1セットにしたモジュールタイプの搬送装置。リニアモーターによるダイレクト駆動と、磁気式アブソリュート位置センサーによる位置検出を採用し、従来のベルトコンベヤーやローラーコンベヤーに比べて高速での搬送と高精度な停止・位置決めを可能にする。
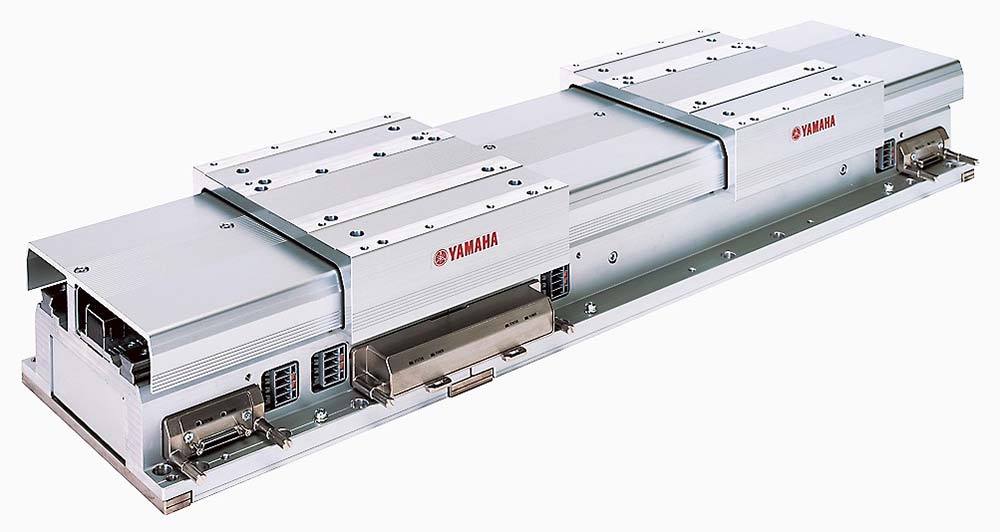
スライダーで部品を搬送するほか、スライダー上での組み立て・加工にも対応する。従来のベルトコンベヤーやローラーコンベヤーに比べて、製造現場などのラインの組み替えが簡単・自由に行える上、高速・高精度の搬送が可能で幅広い業界に適用できことから「次世代工場の搬送プラットフォーム」として注目されている。
ボールねじ駆動では、ねじ軸の固有振動である危険速度とDN値の制限がある。特にストロークに応じて速度を上げることが困難になるが、リニアモーターではこのような制限がないため、ストロークが長くても高速動作が可能になる。非接触構造駆動で推力が発生するため、ねじ軸の回転や転動体の循環による振動が発生しない。そのため、低騒音・低振動を実現できる。また、ボールねじなどで危惧されるグリースの飛散の問題もない。
1軸ベース上に複数のスライダーをセットし、スライダーを個々に制御できる。例えば、1軸ベースにスライダーを6個搭載してそれぞれ動作させることもある。リニアモーターは磁石を接続することで長いストロークにも対応可能。
「スケールレスリニアモーターシステム」は、位置を検出するリニアエンコーダーを使用せず、駆動用のマグネットを磁気メモリーとして磁気センサーで読み取ることができる。リニアエンコーダーを使用しない分、製品コストを抑えることも可能。コストを抑えることにより、従来ラック&ピニオンやベルト駆動で構築されていた搬送用途にも幅広く使用できる。
特に長尺の搬送用途においてはスケールがないため、LMガイドとベースをつなぐだけで簡単に長尺搬送を実現でき、また、モジュール化されているため設計・組み立て工数も削減が可能となる。
高付加価値を備えた汎用(はんよう)性のある工程間搬送の構築が可能。高速、高精度、高速ピッチ動作、スライダー上での組み立て作業、スライダーの逆送動作などにより、高スループットを実現する。
3D金属プリンター
従来難しかった積層造形を実現
3Dプリンター市場が航空宇宙、自動車、金型、医療などさまざまな業種・分野に拡大しているのに伴い、FA、実装関連、産業印刷など電気・電子機器企業も新たに市場に参入している。主に試作製品の製造に活用されてきたが、現在は量産部品を製造できる製品が多数開発されたことでその適用範囲が広がり、製造業における加工プロセスの新しいソリューションとして普及が期待されている。
金属や樹脂を重ねて造形する3Dプリンターは、金型を作らずに設計データから試作品を製作できるだけでなく、従来の加工方法では難しかった構造のデザインや部品の小型化、部品点数の削減などを積層造形によって実現する。
金属を用いる3Dプリンターは、材料供給方式に粉末方式とワイヤー方式の2種がある。粉末方式は金属粉末を平坦に敷き詰め一層ずつ溶融・凝固を繰り返し積層するため、複雑で高精度な造形が可能になる。ワイヤー方式は、熱源に制御性に優れたレーザー光を使用し、造形状態に応じた適切な入熱制御により溶接用ワイヤーを溶融し、3次元構造を高品質に造形する。
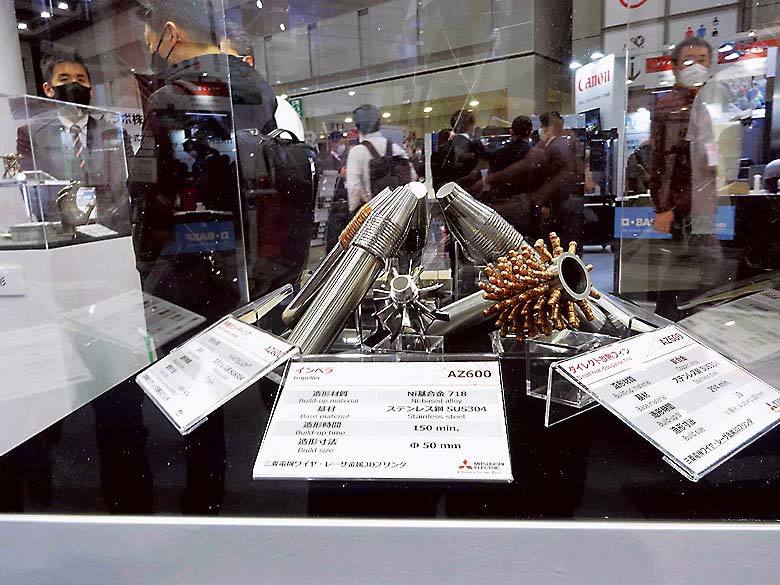
金属3Dプリンターは特許権の関係から欧州が先行。市場も宇宙や航空機、医療などで欧州と北米が中心で、日本は遅れている。今後、例えばEVの製造プロセスの新しい加工機として普及する可能性は高い。海外の工場のプリンターがあれば3DのCADデータを活用して、補修部品などを各地で作ることができる。またプリンターだけではなくCADデータとデジタルツイン技術で、シミュレーションも可能になる。
金属3Dプリンターは樹脂に比べてイニシャルコストが高額になる。顧客からの要望は購入前の造形テストがほとんどであり、受託造形(有償)ビジネスの市場が見込めることから造形受託サービスを始める企業も現れている。また装置納入後は材料供給として継続取引が可能になり、ストックビジネスとしての需要も期待できる。
AMR(自律走行搬送ロボット)
ガイド不要で自律走行が可能
労働力不足への対策として、物流・製造業を中心に人から移動ロボットへの代替が加速している。
ロボットは搬送のみならず、工場・ラインシミュレーションソフトウエアやERP、MESなどのITシステムとつながり、工場全体の最適化・完全自動化などに不可欠なアイテムとなりつつある。
工場や物流の搬送自動化の手段として、AMR(autonomous mobile robot=自律走行搬送ロボット)が注目され、新規参入する企業が相次いでいる。工場や物流などの分野で、すでにAGV(automatic guides vehicle=自動搬送車)が普及している。
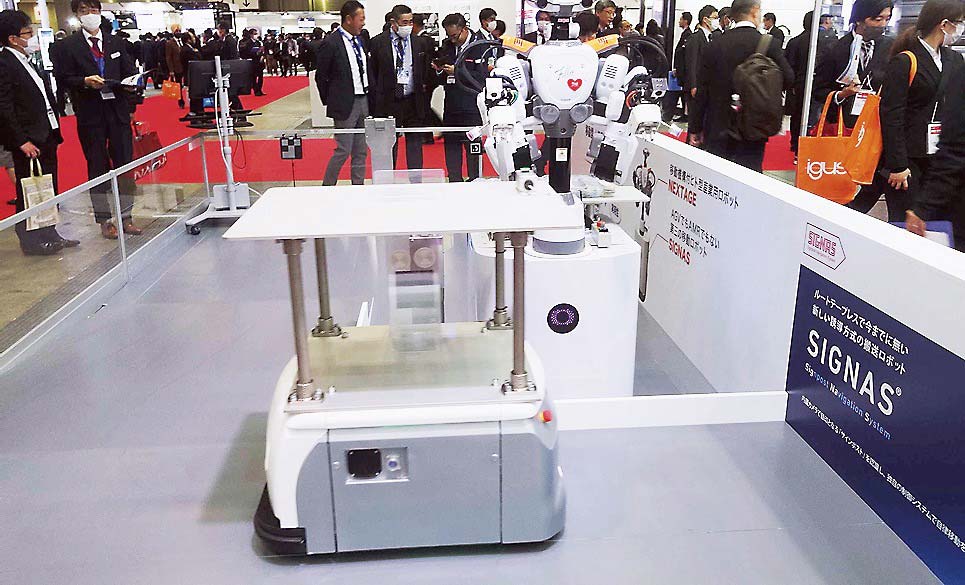
AGVは磁気テープ・ランドマークなどに沿って走行し、障害物があると停止するが、AMRはルートテープ不要の誘導方式を採用し、搬送ロボットマップを基にガイド不要で自律走行し、人や障害物を検知して回避しながら走行する。
製造現場はレイアウトが頻繁に変わり、AGV搬送用ガイドを引き直す必要が生じる。これに対してAMRは拡張性や柔軟性があり、今までAGVでは対応が難しかった少量多品種の製造ライン、レイアウトが頻繁に変わる工程、既存工場などにも導入が可能になる。
AMRはSLAM機能(移動体の自己位置推定と現場地図作成を行う技術)を搭載し、周囲の環境地図を作製し、自己位置を推定・自動で経路検索をしながら自動走行する。拡張性や柔軟性があり、SLAM機能により、実際の走行場所を走らせるだけで地図の自動作成が可能で、既存ラインへの導入も簡単で準備が短時間でできる。
タブレット画面の地図上で搬送先を指示するだけなので、現場での操作性にも優れている。進行方向に障害物を検知するとすぐに停止するため、人との協働も可能で、停止した後は状況を確認してから、自動復帰して回避走行する。地図にない障害物がある場合は、目的地までの別経路を自動で再探索する。
通信プロトコルを用いて稼働中の生産システムや製造ライン、外部設備との連携が可能になる。
産業用インバーター
モーター制御で大幅な省エネへ
産業用インバーターは、産業用モーター(3相誘導電動機)と組み合わせ、モーターの回転数を効率よく制御することで大幅な省エネを実現することから、カーボンニュートラルに寄与する省エネ機器として注目されている。
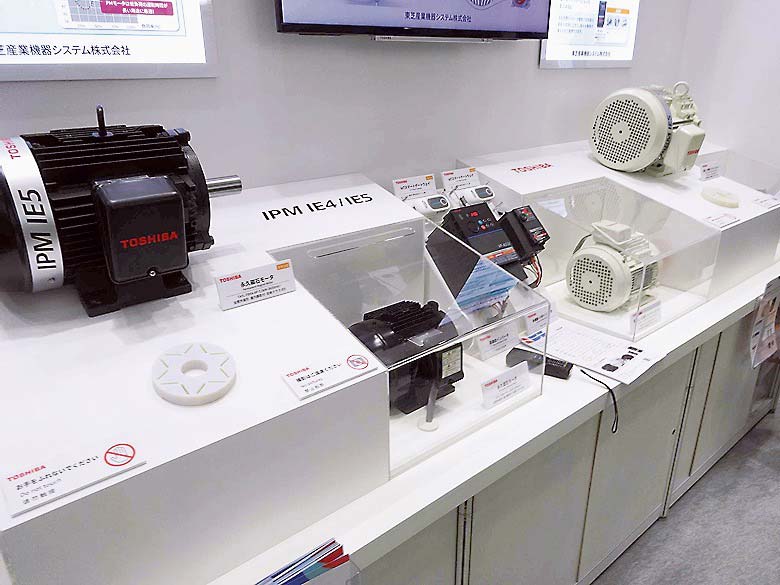
産業用モーターはさまざまな産業機器の動力源として使われている。資源エネルギー庁の調査によると工場はビル空調、生産設備など国内で約1億台普及しており、国内全消費電力量の約55%を占める。同モーターの消費電力を低減することは、カーボンニュートラルの実現に重要な役割を担う。
同モーターは電気を回転運動に変化する際に、内部で一部が熱エネルギーとして消費されてしまう。この損失をいかに低減するかが重要で、世界的にも各国で国際電気標準会議(IEC)が定める規準を採用して高効率化の規制を進めている。日本では「トップランナー方式」と呼ぶ基準が採用されている。
同モーターは一般的に起動時に大きな電力を消費する。産業用インバーターはモーターのON/OFF制御ではなく、モーターに供給する交流電源周波数(商用電源、50/60ヘルツ)を可変し、連続運転しながら負荷に応じたモーターの回転数を制御する。
仕組みは商用電源の周波数一定(日本は50/60ヘルツ)電圧一定(100/200V)の交流を、スイッチングや平滑コンデンサーなどによって直流に変え、その直流を再びON/OFFのスイッチングと変調回路によって滑らかな交流に変える。スイッチングの回数によって周波数が可変でき、直流にすることで電圧も変えられる。
スイッチング素子は現在はIGBT(絶縁ゲートバイポーラトランジスタ)が一般的だが、より高速にスイッチングしてさらなる省エネを可能にするSiCやGaNを採用した製品も登場してきた。産業用モーターは、誘導電動機のほかに、回転子(ローター)に永久磁石を使用した同期モーター(PMモーター=永久磁石モーター)が用いられるケースが増えている。しかし同期モーターは構造上、商用電源をそのまま使うことができず、インバータが不可欠になる。