2022.02.03 【コンデンサー技術特集】ルビコン基板自立形アルミニウム電解コンデンサーの最新開発動向
はじめに
近年、主要国からガソリン車、ディーゼル車の販売を将来的に禁止する指針が示され、自動車メーカーからは、各国の環境規制に対応するためにEVやPHEVの販売比率を増やしていく計画が発表されている。これらゼロエミッション・ビークル(ZEV)に欠かせないものが車載充電器であり、その需要と高性能化は年々高まっている。
車載充電器の一次側平滑用コンデンサーには、リード線形アルミニウム電解コンデンサーに加えて、φ20を超える大形の基板自立形アルミニウム電解コンデンサーも使用されており、高品質を維持した高い性能を実現すべくコンデンサーの製品開発が進められている。ZEVに搭載される電池は、航続距離の延長により高容量化が進められており、車載充電器においては充電時間短縮を目的に高出力化が求められている。このため電源電圧平滑用コンデンサーに対しては、高品質を維持した高リプル品が要求されている。また、多様な使用環境に対する低温特性改善、長期設計寿命に対する特性の長期安定化、燃費向上のための軽量化に対する小形化、などの要求も高まっている。
ここでは、これらの市場要求に対応するための高耐圧用(定格電圧400~500V)基板自立形アルミニウム電解コンデンサーの技術動向について解説する。
高リプル電流化
電子機器に高リプル電流対応したコンデンサーを採用することで、同等のリプル電流のままコンデンサー搭載数を削減することができ、機器の小形化・軽量化およびコストダウンが可能となる。このようなコンデンサーを実現するために、コンデンサーの低ESR化および高放熱化は有効な手段として検討が進んでいる。
<低ESR化>
コンデンサーは、リプル電流が流れるとコンデンサーのESRの大きさに応じて自己発熱する。高リプル化にはコンデンサーの低ESR化が有効であり、低ESR化することによって許容できるリプル電流を大きくすることが可能となる。低密度高耐圧セパレーター、低比抵抗電解液および2タブ構造の採用などによりコンデンサーを低ESR化することができる。セパレーターは、主に天然セルロース繊維で構成され、密度が高く厚いほど耐電圧性能が高くなるがESRは高くなり、密度が低く薄いほどESRは低くなるが耐電圧性能は低くなってしまう。このため、セパレーターの繊維径や密度を最適化することで耐電圧性を損なうことなく低抵抗化した低密度高耐圧セパレーターの採用が進んでいる。
また電解液は、一般的に耐電圧や耐熱性を高める配合とすると電解液の抵抗が高くなることが多く、低温域でのコンデンサーの抵抗増加および容量低下が大きくなってしまう。そこで当社では、薬品メーカーとの電解質開発および50年以上にわたって培ってきた自社電解液配合技術によって、耐電圧性能を損なうことなく低抵抗化した低比抵抗電解液の開発を進めてきた。
さらに、コンデンサーの内部素子の電極箔(はく)から電極を引き出すアルミニウムタブを2枚にすることにより電流パスを短縮し、金属抵抗を低減することによって低抵抗化する2タブ構造も採用している。これらの低ESR技術を組み合わせることで、120Hzで約30%、10kHzで約60%のESRを低減することが可能となった(図1)。
<高放熱化>
前述の通り、コンデンサーはESRとリプル電流とによって自己発熱するため、電源平滑用として用いられる限りリプル電流による自己発熱は避けられない。車載機器は過酷な環境下での使用に加えて、小形化による部品の高集積化や部品点数の削減などによりセット内温度が高くなってきている。アルミニウム電解コンデンサーは、有限寿命部品であり環境温度および自己発熱が高くなると寿命は短くなるため、より効率的にコンデンサーを冷却することでコンデンサーの実使用寿命を長くすることができる。
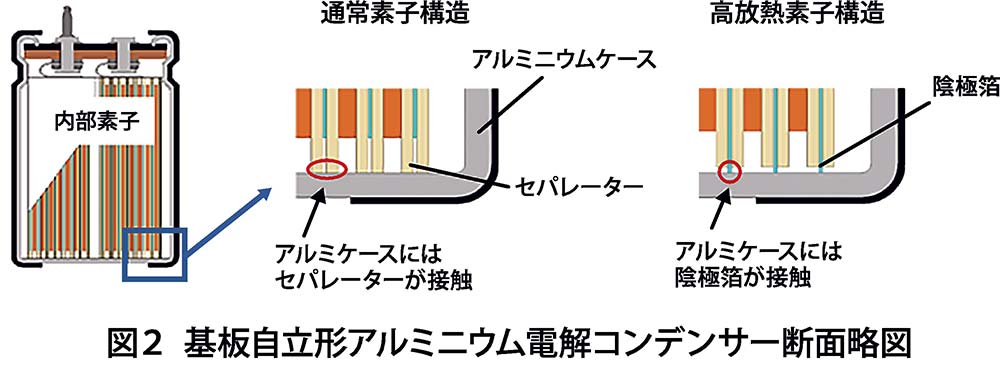
基板自立形アルミニウム電解コンデンサーでは、内部素子のセパレーターが外装材料であるアルミニウムケースに接触している構造が一般的である。この構造を見直し、陰極箔がアルミニウムケースに接触する素子構造(高放熱素子構造)とすることで、コンデンサー内部とアルミニウムケース間の熱抵抗を低減することができ、コンデンサー内部の熱を効率よくアルミケースへ放熱することが可能となる(図2)。例えば、φ35×50Lの製品においては、通常素子構造の場合3.1[K/W]に対して高放熱素子構造では1.6[K/W]となり、約50%の熱抵抗低減効果がある。
また、使用するアルミニウム電解コンデンサーがセットの設計寿命を満足することを検証するためには、コンデンサーの内部温度が重要である。通常は熱電対を用いて実測されるが、あらゆる条件下での実機評価を効率よく実施するためにシミュレーションによる熱分析が行われることが増えてきている。
セット内の冷却手法としては、周囲空気の自然対流による冷却または冷却ファンを用いた強制空冷による冷却方法が多い。このときのコンデンサーの熱モデルは、コンデンサー内部素子と外装ケース間の熱抵抗および外装ケースと外気間の熱抵抗による簡易的な2素子モデルで表すことができ、このモデルで十分運用できていた。
最近では、コンデンサーの外形表面から放熱性樹脂材料を介してヒートシンクや水冷板に放熱する手法が取られるようになってきている。このような冷却方法の場合、コンデンサーの放熱経路が複雑化し、従来の簡易的な2素子モデルではなく多素子による熱モデル化が必要となってきている。当社では、このようなシミュレーション用データの充実も進めている。
最適な静電容量品選定
車載製品は屋外使用が前提であることから極低温下での使用も想定する必要がある。アルミニウム電解コンデンサーの各特性には温度依存性があり、特に低温域において電解液の抵抗の増加による大幅な静電容量の減少ならびにインピーダンスおよびESRの増加が起こる。低温域での静電容量減少およびESR増加は、起動時の電圧オーバーシュート、リプル電圧の増加、発熱増加などの要因となることがあるため、あらかじめ温度依存性を考慮した高静電容量品が選択されていた。しかし、高静電容量品を選択することは、コストが高くなることに加えて製品重量が増えることによる燃費性能悪化の要因にもなることから、低温特性に優れた製品の開発が望まれていた。
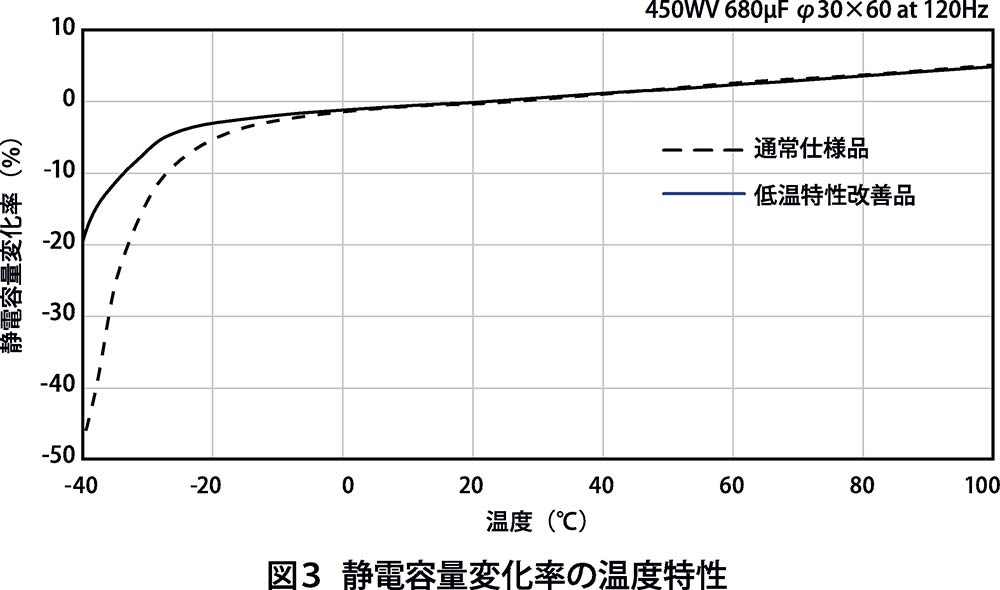
そこで、セパレーターの選定最適化および低抵抗電解液によって低温領域における静電容量減少の改善を進め、-40℃において約30%の静電容量変化率改善が可能となった(図3)。
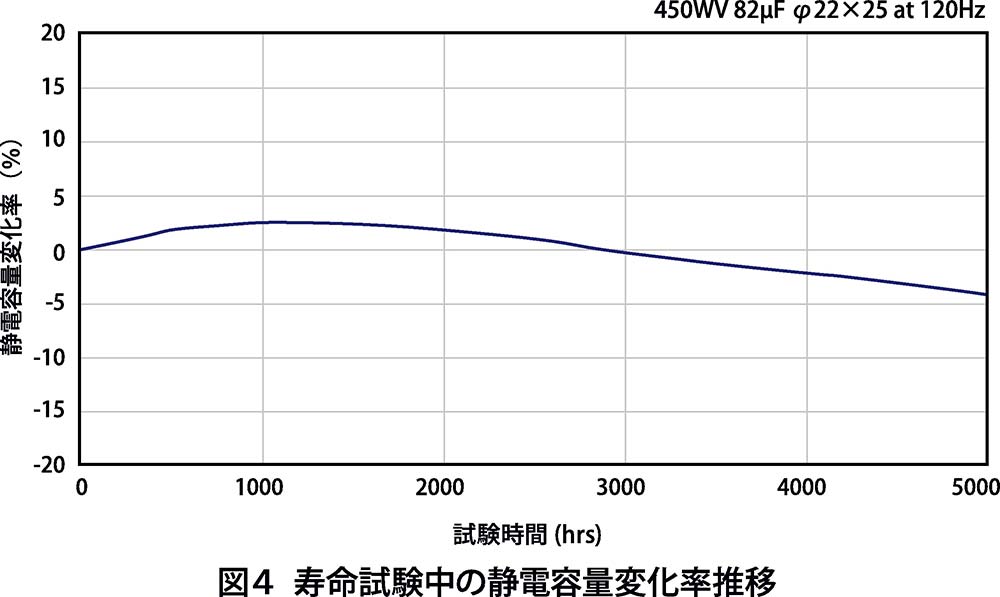
また、アルミニウム電解コンデンサーは、電解液が封口材を介して外部へ拡散しコンデンサー内部の電解液の量が減少することおよび電解液の特性劣化によって、静電容量は低下し抵抗は増加する。一般的に規定寿命経過後の静電容量は、初期値に対して±20%の変化率を規定しているが、長期間にわたり安定性の高い高性能電解液を採用することで、静電容量変化率の実力値を初期値に対して±10%以内に抑えることが可能となった(図4)。
これらを組み合わせることで、初期に必要な静電容量を過大に見積もることなく、適切な静電容量品を選定することで機器の小形化、軽量化、低価格化が可能となる。
高温度保証品および長寿命品の小形化
高温度保証品および長寿命品には、高性能電解液の採用ならびに気密性および耐熱性に優れた封止材の採用は不可欠であるが、小形化に関してはさらに選定セパレーターの最適化および高倍率電極箔の採用が重要である。高倍率電極箔は、エッチングによってアルミニウムの溶出量が増えるため電極箔の強度は低下する。当社では使用する材料に合わせて最適な条件で製造できるよう製造設備を自社開発してきたノウハウを発揮して、強度の低い電極箔を使いこなすことで高品質を保ちながら高容量化を実現している。
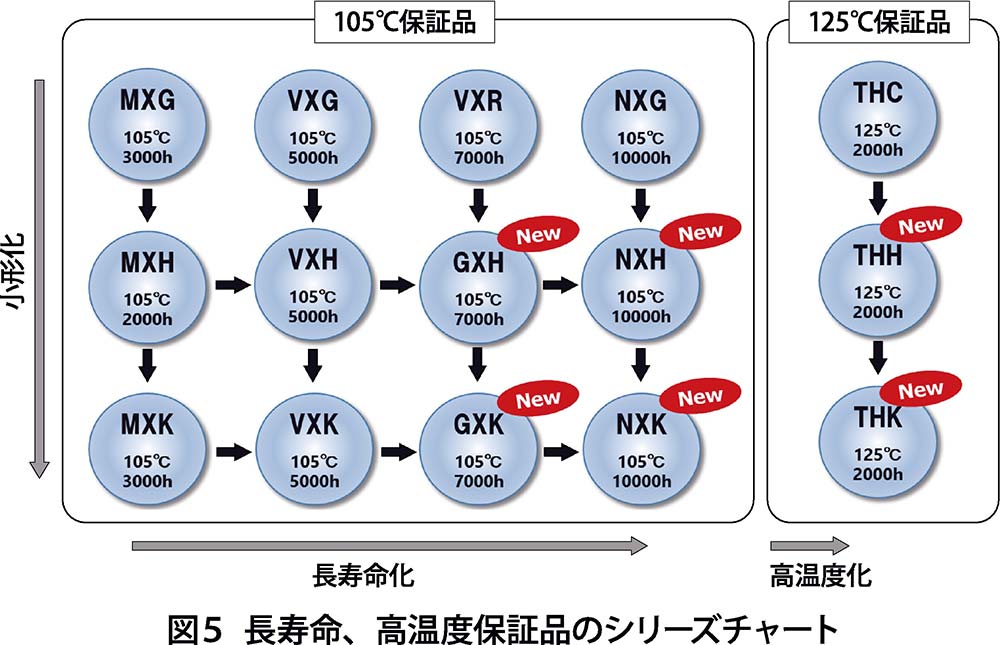
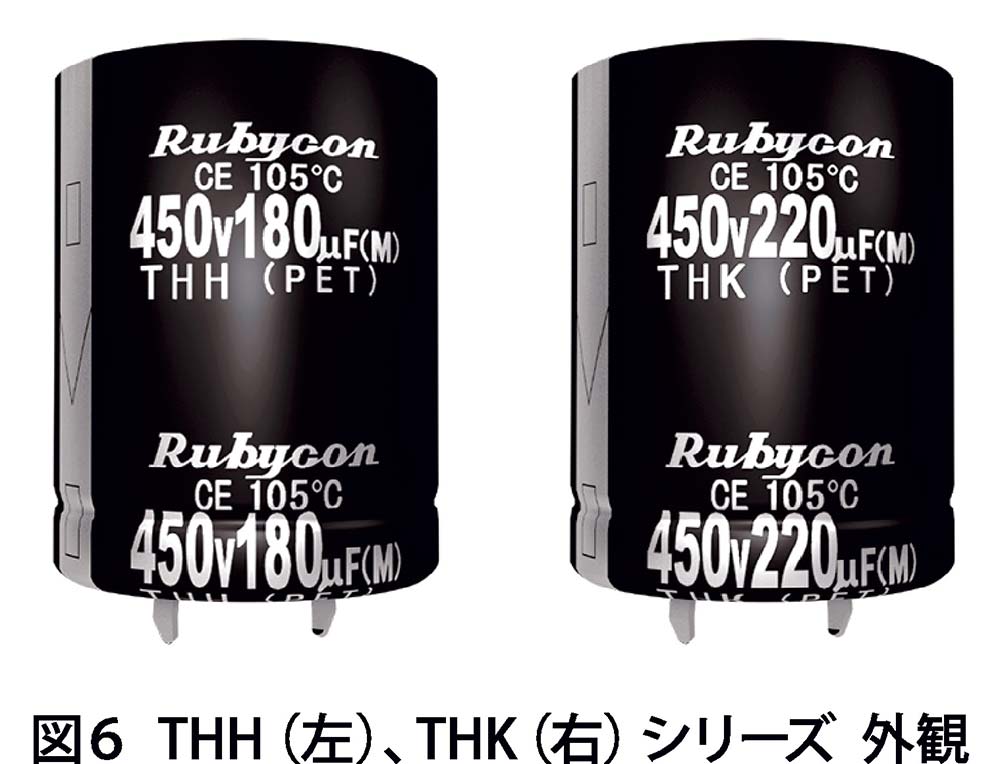
これらの技術を駆使して、用途に応じた最適な性能およびサイズのコンデンサーが選定できるように高信頼性シリーズの拡充を進めてきている(図5、図6)。
おわりに
コンデンサーの市場はますます広がりを見せているが、これに伴って用途によって異なった多岐にわたる要望が寄せられている。今回触れることができなかったリード線形アルミ電解コンデンサー、SMDタイプのアルミ電解コンデンサーおよび導電性高分子アルミ電解コンデンサーハイブリッドタイプを含め、この多岐にわたる要望に応えるべく小形化、高容量化、高温度化、高リプル化、長寿命化などのコンデンサー開発を進めてきている。今後もさらなる高性能化への挑戦が続く。〈ルビコン(株)〉