2023.01.10 【製造装置総合特集】 進化する製造プロセス
EV用モーターなどの銅加工で注目される青色レーザー
第5世代移動通信規格5G、EV(電気自動車)、IoTなどの進展に伴って新たな電気・電子機器が登場し市場を拡大する中、製造技術や製造プロセスが進化を続けている。金属などの接合技術は超音波を利用するものや拡散接合など多様化。EV用モーターなどの銅加工では青色レーザーが注目され、加工機の製品化が進む。半導体後工程ではボンディングなどのプロセスをSMTと融合する動きも現れ、実装機各社が事業化に乗り出している。こうした製造技術の進化は、日本が得意とする「すり合わせ技術」の進化でもあり、これからの動きが注目される。
EV用モーターの銅加工で青色レーザーに関心
レーザー加工
5G、EV、DX、カーボンニュートラルなど新たなトレンドが進展する中、製造現場では、微細な加工を可能にするレーザー加工機がFA・工作機械メーカーから製品化され、本格的な普及を見せ始めている。
レーザー加工は、発振器から発せられたレーザー光をミラー(またはレンズ)で集光してエネルギー密度を高め、金属などのワークに照射して熱加工するのが基本原理。
これまでファイバーレーザー、YAGレーザー、CO₂レーザーなどさまざまな方式の加工機が製品化されてきたが、情報通信機器向け部品や医療機器部品のマイクロ加工など高品質で微細な加工や、炭素繊維強化プラスチックといった難加工材料への要求から、「次世代レーザー加工」への期待が強まっている。
次世代レーザー加工技術の中でも青色レーザーへの関心が高い。
従来のレーザー加工に用いられるレーザー光の波長はCO₂レーザー1万600ナノメートル、YAGレーザー、ファイバーレーザー1064ナノメートルなど近赤外領域が主だったが、青色レーザーは紫外領域の360~480ナノメートルの波長を用いる。
銅、金、樹脂など種々の材料でファインプロセスを実現できるレーザー加工への期待が高まっており、特に、EV用のモーターやバッテリーなどの銅加工においては光吸収効率の高い青色レーザー光源が求められている。青色レーザーによる加工は赤外波長に比べて銅に対する吸収率が高く、とりわけEV開発で多用される銅材料へのレーザー加工に適している。
パナソニック コネクトが開発した青色レーザー加工機は、青色DDL(ダイレクトダイオードレーザー)から放射されたビームを回折格子上に重ね、一つのビームに結合させる独自の波長合成技術を用いて高ビーム品質を保ちながら、高出力でのレーザー光を用いる。銅材料に対して光吸収率が良く、ビーム品質が高いことから、小スポット径で周囲への熱影響が少なく、深い溶け込みの溶接を実現することができるため、電子機器や電子デバイスの精密加工が可能になる。
同社は青色DDLを採用したレーザー加工機の受注を2023年度上期に開始する。
NITTOKUは、EV用モーターの銅巻線の継線工法において、従来のTIG溶接(電気を用いたアーク溶接の一種)に代わる新たなxEV向けモーター用レーザー溶接機を古河電工と共同開発した。古河電工のハイブリッドレーザーをベースにしたもので、EV分野における青色レーザーの実用化が進んでいる。
超音波や拡散方式など多様な技術で用途が広がる
接合技術
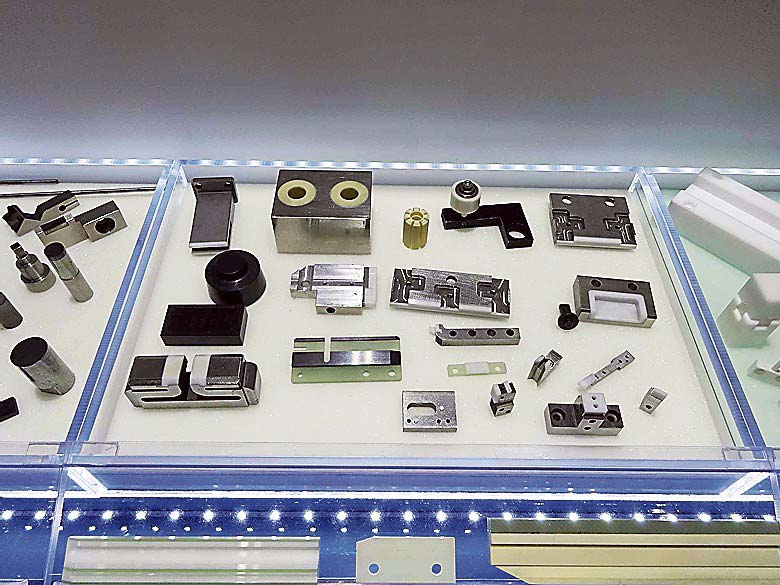
スマートフォンやウエアラブル機器、EVなど新しい電子機器の市場拡大に伴い、新たな製造技術や製造工法が開発されている。電子機器の製造工程で広く活用される接着・接合技術も進化し、例えばスマホやウエアラブル機器は、フレキシブル基板とプリント基板を熱圧着で接続してコネクターレス化したり、組み立てにねじを1本も使わず、接着工法により完成する。
電子機器の製造工程で用いられる接合技術はさまざまだ。金属に電流を流すと発熱する原理を応用した抵抗溶接、レーザー光の集光による発熱を利用したレーザー溶接、金属に超音波を当てて振動による発熱で金属接合を行う超音波接合など多様な方法が用いられ、それぞれが進化を続けている。
例えば真空中で融点以下の温度で加熱、加圧し原子の移動(拡散)によって接合する拡散接合技術では、厚さミクロン単位の金属板を複数枚積層して立体構造(3D)に加工する場合が多く、これまでに100枚程度から、最近では1000層の積層技術が開発された。マイクロ流路を設けた構造に加工してパワー半導体の冷却などの用途が考えられている。
接着技術も進化し、用途が拡大。溶剤(接着剤)を吐出するディスペンサーノズルの微細化技術、制御技術の高精度化により、半導体パッケージングにおけるCSP、BGAでのアンダーフィル剤塗布、ボンディング工程のエポキシ樹脂塗布、液晶パネルのシール剤など、今では半導体分野の接着に広く用いられる。プリント基板にモジュールやコネクターなどDIP部品(リード部品)をはんだを使わずに実装するプレスフィット工法の採用が進んでいる。
EVの軽量化に向け、金属に代えてCFRP(炭素強化樹脂)が用いられるようになり、ここでも接着技術が注目される。
はんだ接合では表面の酸化膜を除去するためにフラックスが用いられるが、樹脂も表面改質によって接着性能を高めることができる。一例では、プラズマを応用し、プラズマの持つラジカルの性質で表面を改質する技術や装置が既に開発されている。
量産部品の製造が可能に 適用範囲が拡大へ
3Dプリンター
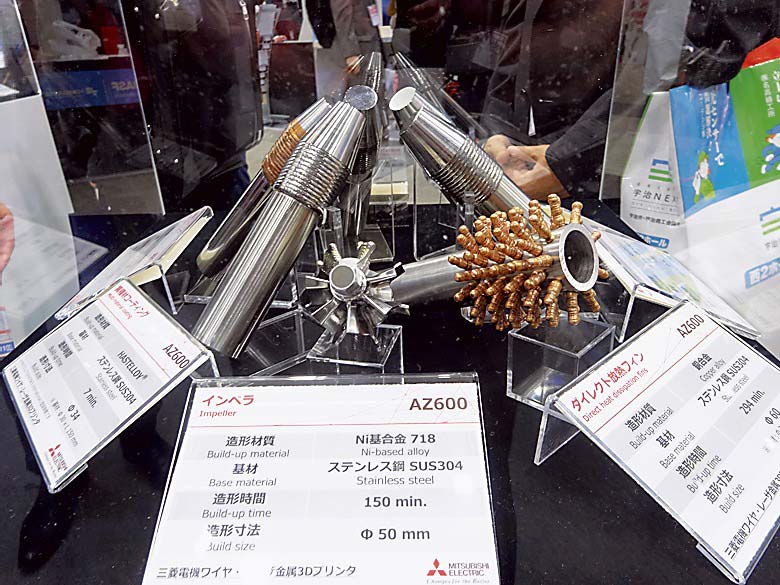
金属や樹脂を重ねて造形を行う3Dプリンターは、金型を作らずに設計データから試作品を製作できるだけでなく、従来の加工方法では難しかった構造のデザインや部品の小型化、部品点数の削減などを積層造形によって実現可能になる。
3Dプリンターは欧米が先行し、主に試作機として活用されてきたが、現在は量産部品を製造できる製品が数多く開発されたことから、適用範囲が広がりをみせている。市場規模はグローバルで年間1000億円といわれ、2030年には1兆円産業に成長すると予測されている。
金属を用いる3Dプリンターの材料供給方式は粉末方式とワイヤー方式の2種がある。
粉末方式は金属粉末を平坦に敷き詰め、一層ずつ溶融・凝固を繰り返して積層するため、複雑で高精度な造形が可能。
ワイヤー方式は、熱源に制御性に優れたレーザー光を使用し、造形状態に応じた適切な入熱制御により溶接用ワイヤーを溶融して3次元構造を高品質に造形する。
三菱電機は19年に粉末方式で金属3Dプリンター市場に参入し、22年にはワイヤー方式も発売した。医療機器や自動車、エネルギー関連の金属部品の製造など産業用途を狙う。
FUJIは、3Dプリンター市場に19年に参入し、全く新しいコンセプトの装置「FPM-Trinity」として開発している。
FPM-Trinityは樹脂3D造形、電子回路の印刷、部品実装が可能なオールインワン装置。マスクやジグが不要なため、少量多品種、カスタム品の製造が容易に行える。通常の電子基板では作れない形状の電子デバイスの製造が可能だ。製品化に伴いFPM-Trinityを利用した電子モジュール試作サービスを実施中で、回路図と部品表(BOM)を用意するだけでモジュールを試作する。
ミマキエンジニアリングは、長年培ってきたインクジェット技術、UV硬化インク技術を駆使してフルカラー3Dプリンターの機種拡充を進めている。同プリンター事業を中長期成長戦略の一環に掲げて17年に発売した1000万色フルカラー「3DUJ-553」を皮切りに、熱融解積層方式、1.8メートル大型造形モデル、1000万色フルカラーエントリーモデルなどラインアップを拡大している。
フルカラー3Dプリンターは、立体物の造形動作と同時にフルカラーでの表面印刷動作を行い、彩度の高いフルカラー着色立体物の造形を可能とした。また、アクリル系UV硬化樹脂で造形するため機械的な強度が高いだけでなく、表面のカラー領域が厚いため退色・消色しにくい。
各社、融合化を視野に製品拡充やM&Aを推進
半導体後工程とSMTプロセスの融合
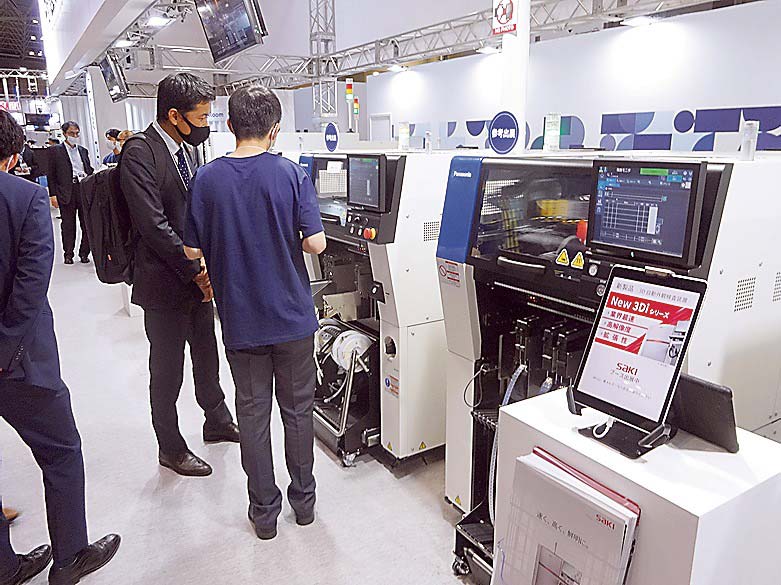
これまでのチップ上に描く(露光する)回路の線幅を小さくして集積度を高める前工程の微細化技術は、物理的にも限界に近づいており、高機能化や多機能化を継続していくために後工程の重要性が高まっている。
半導体の製造プロセスの後工程ではSiP(system in package)のようにメモリーやマイコンなど複数のチップをパッケージ内で3次元方向に積層して実装する3D実装や、異なるプロセスノードを使用してチップを製造、集積化するチップレット技術など、パッケージング技術による高集積化が進む。
3次元実装は基板との接続に貫通電極(TSV)とバンプ(はんだボール)を用いるフリップ実装が増え、複数のベアチップや受動部品などを搭載して一つのICとしてパッケージングするMCM(マルチチップモジュール)も増加。これらボンディングなどの製造プロセスにはSMT(表面実装技術)が応用されるケースが増えてきた。
実装機各社はこうした半導体製造プロセスに着目。SMTと半導体製造プロセスの融合を念頭に置いた製品拡充やM&Aによる事業化を進めている。
FUJIは、2018年8月にダイボンディング装置を主力とする半導体製造装置メーカーのファスフォードテクノロジ(FFT、山梨県南アルプス市)の全株式を取得した。電子部品実装ロボットで培ったFUJIの独自技術とFFTの半導体関連技術の連携を進める。SMTで扱う部品が極小化し、半導体デバイスも増加する中、ボンディングのプロセスに近接したSMTプロセスの必要性も高まっている。
ヤマハ発動機は、同社を親会社に半導体ボンディングを主力事業とする新川(東京都武蔵村山市)、モールディング装置のアピックヤマダ(長野県千曲市)、半導体検査装置のPFA(埼玉県坂戸市)の事業統合によりヤマハロボティクスホールディングスを19年7月に発足。次世代ボンディング技術「ポスト5G向けチップオンウェハダイレクト接合3D積層統合技術」の開発を進める。
JUKIは半導体後工程とSMT工程の融合も視野に入れ、FPDや製造装置・半導体パッケージ製造装置企業のAIメカテックと22年9月に資本業務提携を結んだ。
AIメカテックはファブレス企業で、約5年前からFPDや製造装置や半導体パッケ-ジ製造装置、はんだボールマウンターの生産を、JUKIがグループ事業として展開するJUKI産機テクノロジー(秋田県横手市)などに委託していた。両社が有する技術領域や業界情報の共有による新たな事業領域の創出を進める。
パナソニック コネクトプロセスオートメーション事業部は「回路形成プロセス」(電子部品実装機、半導体製造装置、ディスプレー製造装置、ソフトウエア)と「熱加工システム」(溶接機、溶接ロボット、レーザー加工ロボット)の2分野を主事業としている。半導体製造プロセスでは実装業界に先駆けてドライエッチャー、プラズマダイサー、液晶ボンダー、ダイボンダーなどを製品化した。