2022.11.25 【はんだ総合特集】はんだ付け装置動向
低消費電力、低N₂などが進むリフロー装置
表面実装技術による製造工程のはんだ付けは、フロー装置、リフロー装置が用いられる。後付け部品などにはんだ付けロボットの普及が進んでいる。
フロー/リフロー
「真空リフロー」の需要増加消費電力量、窒素使用量削減
フロー装置は、はんだ槽に溶かしておいたはんだの表面層に基板の下面を浸すことによって、はんだ付けを行う方法。主にリード線の付いた部品に使用する。表面実装部品を両面実装する場合にも使われる。はんだ槽は、はんだ液面に波を立てる噴流式と、液面を動かさない静止槽(DIP方式)がある。
リフロー装置は、クリームはんだを印刷した基板に部品を搭載後、はんだ槽で基板の上下から熱風や赤外線で加熱してはんだを溶融、自然冷却して部品と基板を接続する。
はんだ付けする時にはんだの表面が酸化すると接合が十分にできなくなるため(はんだのぬれ性と呼ばれる)、大気中の酸素を不活性化させる窒素ガス(窒素分子=N₂)が用いられることが多い。
環境への影響と工程の短縮から、フラックスを使用しないフラックスレス実装が注目されている。
リフロー実装では、フラックスを用いて金属表面の酸化膜を除去し、ぬれ性を確保するため、リフロー後に溶剤で洗浄する必要がある。フラックスレス実装では、酸(ぎさん)を用いた蟻酸雰囲気加熱で、蟻酸の酸化還元効果により金属表面の酸化膜を除去し、フラックスレスでも高いぬれ性の確保ができる。フラックスレス実装では、リフロー後の洗浄工程が不要となり、環境負荷を低減できる。
はんだ付けでは、接合部のボイド(はんだの中に気泡が入ることで発生する付き不良)の発生を抑えることが重要な課題になっている。ボイドははんだ表面の金属酸化、はんだ溶融中にガスが残留など、さまざまな要因から発生する。そのため、リフロー工程を真空中で行う「真空リフロー」の需要が増加している。
リフロー炉内雰囲気の循環効率を向上させ、断熱構造の強化で安定時の消費電力量削減、立ち上げ時間短縮、窒素使用量削減、フラックス回収など改善が進んでいる。
はんだ付けロボット
レーザーや超音波で自動化 グローバルに需要が拡大
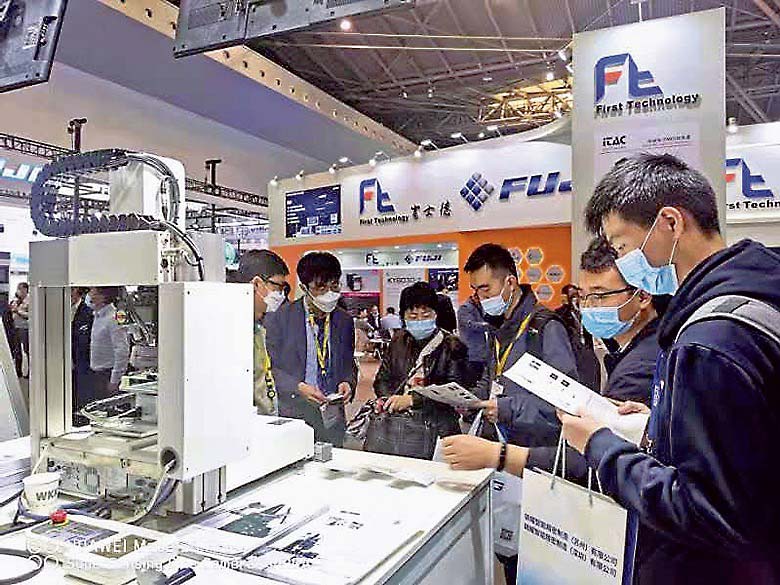
表面実装では困難な大型電子部品などのはんだ付けは、リフロー工程後にはんだごてを使って手作業で行っていたが、最近はレーザーや超音波を応用したはんだ付けロボットによる自動化が進み、需要がグローバルで拡大している。
レーザーはんだ付けロボットは、レーザー光をレンズまたはミラーで集光し、高パワー密度、高エネルギー密度の熱源として利用する。そのレーザービームを加熱したい対象物に当てて加熱する。対象物の加熱温度はレーザー光の入射側の条件(レーザーパワー/レーザーエネルギー/波長)と加熱したい対象物の放射率(吸収率)や熱容量・比熱などのさまざまな条件の組み合わせにより決まる。
はんだ付けは多くの場合、二つの部品をはんだで接合することが目的のため、その二つの部品の加熱温度が均等でないと、はんだのぬれ広がる範囲も均等にならない。異なる材料同士の加熱温度が均等になるよう、レーザービームの形状や照射位置などを最適化することが重要になる。
糸はんだ供給の場合、あらかじめはんだ付けしたい箇所(多くは電極部)へレーザー照射(事前加熱)を行い、糸はんだがはんだ付け箇所へ接触した際に抵抗なくぬれ広がらせる。ペーストはんだの場合は、はんだ付けしたい箇所へペーストはんだが事前に塗布されているため、はんだ供給までの事前加熱はできず、徐々にレーザーパワーを高める加熱プロセスが用いられる。
レーザーはんだ付けは、非接触によるはんだ付けができることが最大の特徴で、基板にも電子部品にも一切触れず、レーザー照射とはんだ供給だけで物理的負荷を掛けることがない。ピンポイントで効率的に加熱できるのも大きな強みで、こて先が入らないような狭い場所や高密度実装で隣の部品と距離がない場合でも角度を変えるなどして照射できる。
超音波はんだ付けシステムは、ヒーターで加熱したこて先から約60キロヘルツの超音波を発振しながらはんだ付けを行う。振動子によって発振された超音波がホーンを介してこて先に伝わり、はんだ付け母材と溶融はんだの境界付近にキャビテーションによる泡を発生させる。
キャビテーションの爆発力によって酸化物の表面を改質し、汚れや酸化被膜などを除去し、同時にはんだと母材の溶解・拡散作用によって拡散層を生成する。超音波のキャビテーション効果により発生した空洞が潰れる瞬間、酸素を取り込むと同時に熱エネルギーを放出する。
そのエネルギーを活用し、溶融した酸素親和力の強いはんだの金属元素が、取り込まれた酸素を媒介として、ガラスなどの表面と共有結合を行う。